Home > Explore Careers > In The Workshop > Mounter
As a mounter, you are integral to the workshop’s production of handcrafted fine and high jewellery, generally using traditional handcrafting techniques.
You must have an inherent meticulous attention to detail and impressive
diamond mounting skills (think back holing, gallery work, fine claw work and precision soldering). As a mounter, you also carry out other manufacturing tasks: cleaning and assembling castings, resizing, polishing and custom or bespoke work and repairs.
You also are likely to
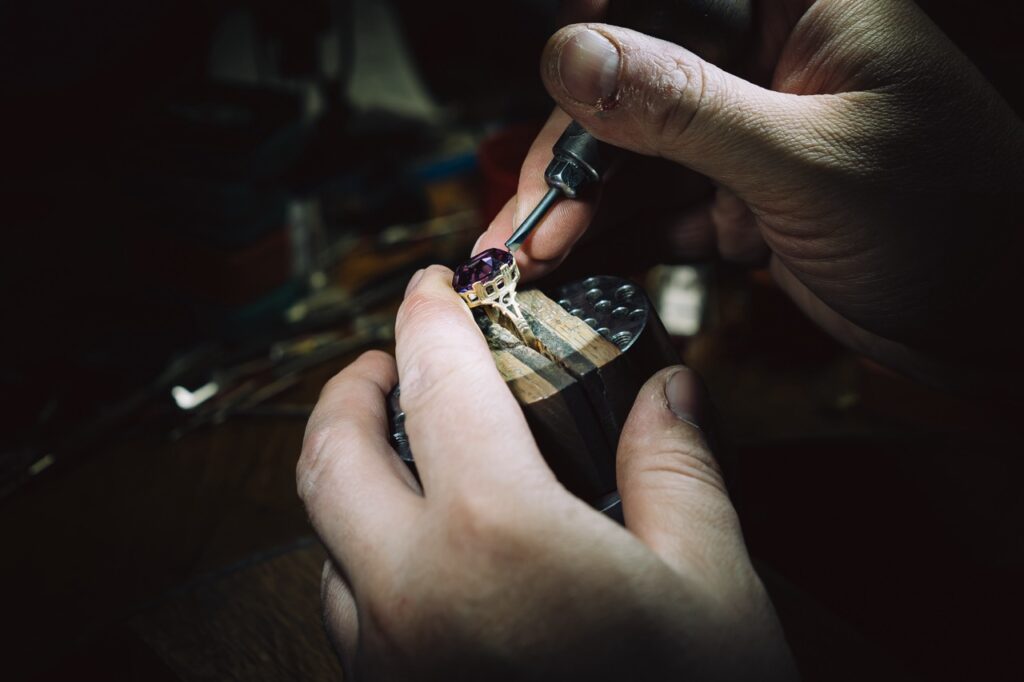
Length of Training
3-5 Years
Salary Expectations
£20,000+
Qualification Requirements
Experience
You must have 3 years + experience at the bench.
Knowledge
Skills
Personal Attributes
Qualification Requirements
You must have a technical background, either a specific mounting apprenticeship, technical training foundation or HND.
Role Also Called
Diamond mounter, Gemstone mounter, Fine jewellery mounter, Apprentice mounter
Experienced mounter, Senior mounter, Goldsmith, Jeweller, Jewellery mounter, Jobber, Repair and restoration jeweller
Meet the Mounter
Insights from Darren Sherwood, acclaimed goldsmith and mounter.
Question
Why did you decide to work in the jewellery industry?
Answer
Since childhood, I always knew I wanted to get into art of some description. Returning to England after growing up in Trinidad, I buried myself in art and did my foundation course at Central Saint Martin. Initially, I wanted to do sculpture or animation, so I specialised in sculpture, product design and jewellery. I tried sculpture and sucked on an epic scale – I do not have the mindset of a fine artist.
My tutor suggested I try jewellery – he thought it would better feed my technical perfection gene. He was right. I’d never thought of jewellery before this. I did my BA(Hons) at Kent Institute of Art and Design (KIAD) in jewellery/goldsmithing and silversmithing. I just lived in a workshop for three years and got as much work experience with workshops such as Padgham & Putland and Grant Macdonald; this gave me an insight into what the trade was like and what was expected. When I finished my degree, my tutor sent me a job application for a mounter in the West End – my step into fine jewellery.
Diamond mounting was quite a learning curve. I worked during the day and got home to practice on a homemade bench in my bedroom every night. The need for accuracy and the aim to get as close to perfection as possible was a perfect fit for me. Everything is scrutinised – finish, angles, backholes, filing, soldering, and the amount of solder used. It was a kind of masochistic education; never really happy with what you create.
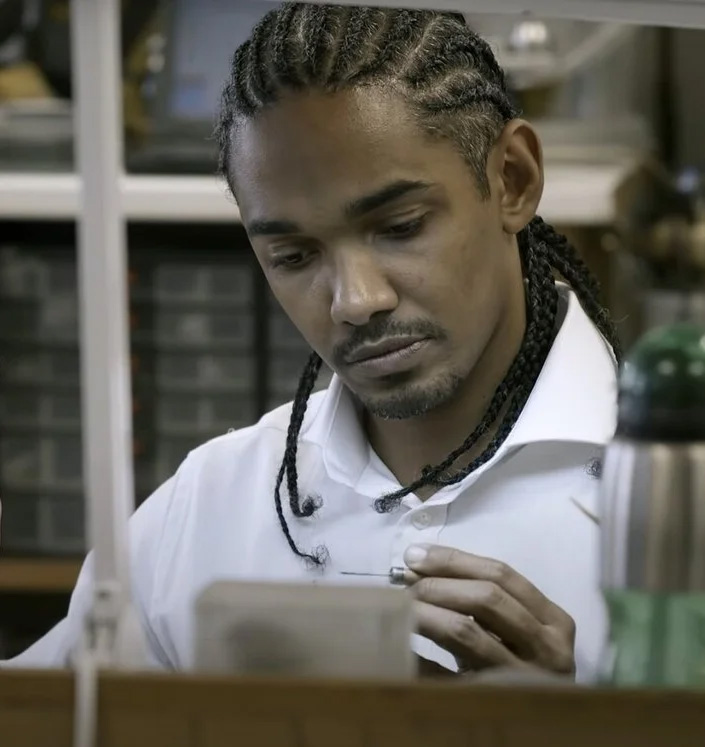
Question
What is the best thing about your job?
Answer
You can get lost in the job; it’s a very lucky position to be in. You get to do what you love and sometimes make money from it. It’s a nice thought that you may be creating future heirlooms or at least a piece that will far outlive us all for future generations to appreciate. Since opening Sherwood Jewellery, my shop in Purley, I’ve come to appreciate the repairing or re-modelling of family heirlooms – it’s nice to see the happiness sentimentality brings. I’ve had people in tears hugging and thanking me on the shop floor for my craftsmanship. Something you rarely get when working in the high-end market or for a workshop- a bonus to being customer-facing.
Question
What advice would you give to somebody wanting to become a mounter?
Answer
First off, build a workbench in your room/house. So many people come to me and ask me for advice; I first ask if they have a bench at home. If you want to learn to make, you’ve got to put the hours in. Watch videos on YouTube, read books, try it out, make mistakes, and push on through. Check in with the Goldsmiths’ Company as they are dedicated to passing on the knowledge, and give loads of courses for free. Even if you have to pay, those courses are worth their weight in gold as they are vetted and taken by respected tutors/makers/designers from within the trade.
If you are in it for the money, look elsewhere. Diamond mounting is more about the art and the crafting of metal. If you’re not in it for the love of it, you’d never put the hours in that are needed.
There are a lot of routes you can go down – many are tempted by CAD at an early stage, but please try not to do it until you are somewhat proficient at the bench. People use me for CAD because I CAD things how I’d hand make them. And I am very detailed in my CAD work—proportions, thicknesses, curves, points, setting edges, cleaning up percentages, etc. Although your CAD drawing may look amazing, it may not be transferrable into metal.
Question
What has been a career highlight for you?
Answer
It was going self-employed. It was a scary jump after being employed and having a young family at the time, but with my usual optimistic outlook and zero planning, I took the leap, and it worked out all right. I’ve been approached to work on some fabulous pieces and met some fantastic people on the way. I got to meet The King as well; that was pretty cool.
I was asked to do a workshop for the Jewellery Valuers Association, which was great – some seriously knowledgeable people. Last year I gave a presentation on the big stage, which was somewhat terrifying but great fun, and it led to me being invited to present a talk at the International Coloured Gemstone Association’s bi-annual conference in Dubai earlier this year. I met a part of the trade I never knew about – the miners, the labs, and some great people from GIA and Gem-A. My phobia of public speaking had to take a back seat real fast. Also, I have been accepted into Week Two of the Goldsmiths Fair this year; that’s very exciting.
Question
Have you undertaken additional training?
Answer
I’ve learned on the job. Countless hours of trial and error, reading, watching videos and tutorials, and asking advice from the elders or more experienced in the trade. I did do a setting course with Jura in Holland. But when I got into the trade, things were a lot different, and the 2008 crash also forced a huge change within the industry. There aren’t many good courses out there, from what I’ve seen, for beginners or experienced makers.
However, The Goldsmiths’ Company and, recently, the Goldsmiths’ Centre have been an incredible help over the years. I met Peter Taylor [Goldsmiths’ Centre director] back in Uni, and he used to check up on me and my progress wherever I went. If I needed some advice and he couldn’t help, he always knew who to put me in touch with. I have loads of time for the Goldsmiths’ Centre – it’s a body that is dedicated to passing on the knowledge and helping jewellers and their businesses survive and grow.